
All About Desiccants
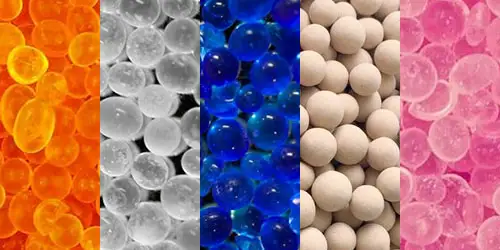
A desiccant is a highly hygroscopic (moisture collecting) material that attracts water molecules in the air and holds them. They are widely used to create a dry environment inside a sealed container, from small pouches holding lateral flow devices to massive cargo shipping containers. There are many different desiccant substances, with clay, silica gel, and molecular sieve among the most commonly used. Desiccants also come in a number of formats, including small breathable packets, rigid plastic containers, drums of bulk desiccant, and desiccant paper. The type, format, and quantity of desiccant needed for a specific application depends on many factors, such as:
- Volume - The quantity of air inside your sealed package or container
- Product - Different items may require moderate to extremely low RH (relative humidity)
- Container - How easily air or moisture can flow into the controlled area
- Environment - Locations in which high humidity, condensation, or extreme temperatures occur
- Other Factors - Any other considerations, including timing and chemical compatibility
Understanding the Right Desiccant for Your Application
When evaluating desiccants, it is important to keep the following questions in mind:
• What is the desired relative humidity for your product?
• How wet is your product (residual moisture)?
• What type of package are you attempting to desiccate?
If you are using a pouch that has a high water vapor transmission rate (WVTR) you may want to increase the amount of desiccant used to accommodate the higher amount of water vapor that will be transmitted through the film over the course of the package's lifetime. How long do you plan on the product being packaged? When a long shelf life is desired you need to take into consideration the type of container and calculate the amount of water vapor that will be transmitted through the container wall (if any) and adjust accordingly. What is the volume of the area you are working with? If you have a large amount of interstitial space (amount of space between the product being packaged) or a lot of headroom (amount of space between the top of the product and the top, sealed area of the container) you may want to increase the amount of desiccant to compensate for the increased volume. Is this product going to be consumed? If so, you may want to evaluate a clay or non-indicating silica gel desiccant for products such as these. Do you want to be able to re-use the desiccant after it is saturated and can no longer adsorb moisture? If so, you may want to consider clay and silica gel. Both desiccants are able to be regenerated in an oven when in their bulk form.
Desiccants vs. Oxygen Absorbers
We are often asked whether desiccants or oxygen absorbers are the appropriate product for a specific application. Simply put, desiccants remove moisture from air and oxygen absorbers remove oxygen. For example, plastic biopolymers often require a nearly 0% RH environment to prevent hydrolysis, and desiccants should be used; with food products such as jerky, oxygen absorbers are advised to inhibit the growth of microbial organisms that require oxygen. It is usually inadvisable to combine desiccants and oxygen absorbers because most O2 scavengers require moisture to work properly, but our sorbent experts can suggest formulations that will work jointly.
The table below outlines the capabilities of the various desiccants IMPAK offers. If your application calls for a desiccant not shown here, such as activated alumina, activated carbon, metal salts, or phosphorus compounds, contact us so that one of our experts can put our 30+ years of desiccant expertise to work for you.
Note that IMPAK recognizes that organizations, product developers, and package engineers understand that 90% RH, even 40% RH, is unwanted for most packaging scenarios. Leading semiconductor and glucose test manufacturers, for example, are generally looking to maintain an RH of 5% or less.
Type of desiccant → | Silica Gel | Clay | Molecular Sieve | Calcium Oxide | Calcium Sulfate |
---|---|---|---|---|---|
Max. adsorptive capacity by weight (77°F, 90% RH) | 40%✔ | 25-31% | 25% | 32% | 10% |
Adsorptive capacity at 77°F, 30% RH | moderate | moderate | moderate | high✔ | low |
Adsorptive capacity at 77°F, 10% RH | low | moderate | high✔ | high✔ | low |
Time to reach adsorptive capacity (77°F, 75% RH) | ~6 hrs✔ | 10-12 hrs | ~5 hrs✔ | 36-48 hrs | ~4 hrs✔ |
Optimal effective RH range | 50-90% | 20-80% | 0-90%✔ | 0-90%✔ | 60-90% |
Resistance to desorption at high temperatures | low | low | high✔ | moderate | moderate |
Can be regenerated? | yes✔ | yes✔ | yes✔ | no | no |
Water Capacity of Various Sorbents at Different Relative Humidity Levels
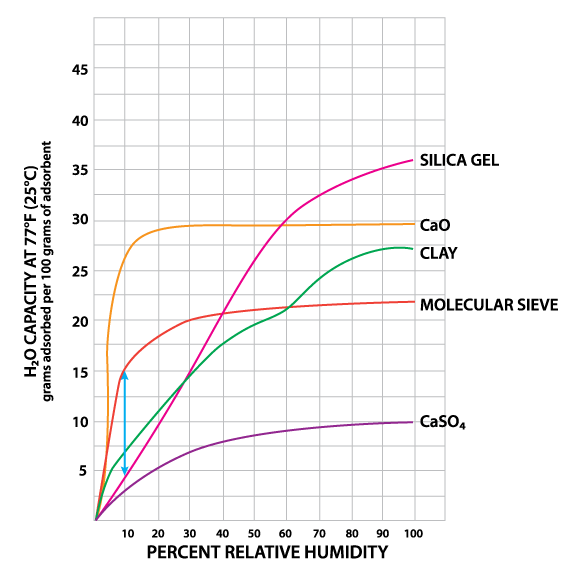
This graph clearly demonstrates the key factors in making a decision on which sorbent is most appropriate for a number of applications. By way of example, this is a graph that clearly shows how both calcium oxide and molecular sieve have some of the highest capacities at low relative humidity levels.
If your target relative humidity for your product (e.g., a lateral flow device, a printed circuit board, a sophisticated piece of electronic equipment) is less than 10%, then this graph clearly shows that with molecular sieve you are getting more than twice the “product” on a gram for gram basis than you are with silica gel. As an industry leader in providing the full range of sorbents, we know how important it is to understand your particular application and how critical it is to answer these questions:
”What relative humidity do we want our product not to see?”
“What level of relative humidity should we ensure that our product never sees?”

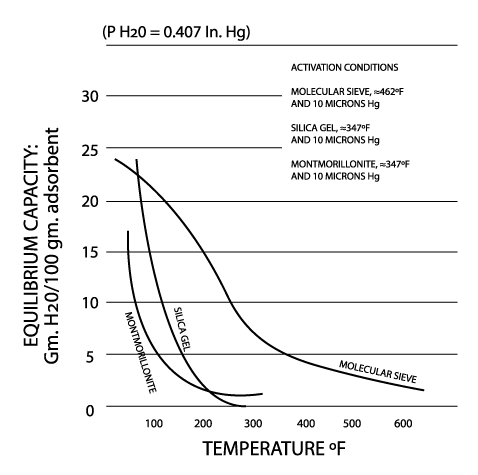
No, "Adsorption" Is Not Misspelled
Nearly all of the desiccants IMPAK offers work via adsorption as opposed to absorption. In other words, when moisture is adsorbed by a desiccant, water molecules are drawn from the air and become stuck to the surface of the desiccant media, similar to how a magnet will cause ferrous materials to become stuck to its surface. Absorption, on the other hand, involves one substance combining with another, such as when water is added to dry gelatin. In fact, oxygen absorbers, true to their name, function by drawing O2 into absorptive media by means of a chemical reaction.
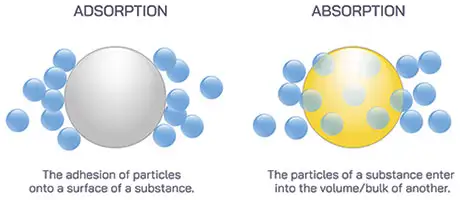
When deciding which desiccant is best for your purpose, keep in mind that some desiccants are prone to desorption - releasing the moisture they have adsorbed - if exposed to excessively high temperatures. Clay desiccant is likely to desorb starting at ˜120°F (˜50°C) and silica gel at ˜150°F (˜66°C). Molecular sieve desiccants resist desorption up to temperatures of ˜300°F (˜150°C), making them well-suited for use in a wide range of temperatures. This is one of the reasons why many agree that molecular sieve is the best desiccant available.
Molecular Sieve Is the Best Desiccant
Reusability
Given that some desiccants will release their moisture (desorb) at high temperatures, some users advocate for re-using desiccants by drying them out with heat, often in an oven. This process, called recharging (or reactivating or regenerating), is possible for some forms of desiccant, such as desiccant paper and bulk desiccant granules, including those in the DriBox. Customers are strongly advised NOT to attempt drying/baking desiccant packets, since they are usually packed in Tyvek®, which will deform and start to shrink at around 212°F (100°C) and melt at higher temperatures. Additionally, there is no guarantee that desiccants will retain their full adsorptive capabilities after recharging, and it has been noted that said capacity diminishes after repeated regeneration cycles. The time, effort, and literal energy required to recharge desiccants makes the process unfeasible in many circumstances, and due to the many factors that could affect results, IMPAK can only recommend it for certain products. Contact us to learn more.
How Does Moisture Cause Damage to a Product?
Moisture trapped within a product package or leaking into it during storage and shipping can cause many harmful effects. The stability of many pharmaceutical formulations and diagnostic reagents, as well as the maintenance of their physical product integrity, is often closely tied to the moisture conditions of the package environment.
In unsterile or poorly sterilized situations, moisture can promote the growth of mold, mildew and fungus. Products using some polymers are prone to swelling in high humidity conditions as intermolecular bonding between polymer chains can be weakened by the presence of water. In some cases water can become an integral part of the bulk crystal structure of a product through the formation of hydrates. If a solid is very water soluble, such as a sugar coating, and the right conditions exist, dissolution into the sorbed layer can trigger irreversible water uptake and subsequent deliquescence.
In the case of electronics, the presence of moisture can cause not only corrosion but also can lead to "short" circuits, wherein the electricity powering the device reroutes through the water instead of its assigned conductive path. These will not necessarily lead to cinematic instance of panels blowing open and sparks flying. In fact, they will usually be much more subtle and untraceable by making the device's operation unreliable. Sometimes it works... sometimes it doesn't. At the very least a situation like this is frustrating; at worst, life-threatening.
How Do Desiccants Work?
Most porous adsorbents, such as silica gel, activated clay, or molecular sieves rely upon physical adsorption rather than chemical adsorption to accomplish their task. Physical adsorption involves relatively weak intermolecular forces (van der Waals forces and electrostatic interactions) between the moisture and surface of the desiccant.
Chemisorbents, such as calcium oxide, involve an actual chemical bond. Physical adsorption of moisture is typically exothermic. The strength of the adsorptive bonds can thus be measured by the heat of adsorption. The higher the heat of adsorption for moisture on the desiccant, the stronger the bonding and the less easily that moisture can be subsequently removed.
In a porous desiccant such as the silica gel used by DriBox, water is removed from the airspace by:
1) multi-layer adsorption, which is the attraction of thin layers of water molecules to the surface of the desiccant. Because the desiccant is very porous, the surface area is high and significant amounts of water can be attracted and adsorbed;
2) by capillary condensation in which the smaller pores become filled with water. Capillary condensation occurs because the saturation water vapor pressure in a small pore is reduced by the effect of surface tension.
How Do I Know It's Working?
The ultimate test of a desiccant is a container free from moisture or a product in perfect condition. But for situations in which it is imperative to have data that confirms how well your desiccants are working, IMPAK provides many options.
Indicating Silica Gel is a popular option. Whether in small packets, in the reusable DriBox, or in bulk, indicating silica changes color, either from blue to pink or from orange to green, when saturated with moisture. IMPAK also offers indicating molecular sieve. These products provide an easy way to visually confirm basic effectiveness, though they do not provide data about RH levels in the sealed environment.
Humidity Indicators are cards with colored dots or spots that, when sealed in a package with a desiccant, will change color according to how much humidity is in the package. There are different humidity indicating cards for registering different RH levels, from below 8% to a range from 30% to 80%. One limitation to these cards is that your packaging must allow visibilty, either with a window or fully transparent material. IMPAK is also proud to offer the Humonitor™, a device that attaches to a pouch to show interior RH with a humidity indicator that is visible on the outside.
For those who require the most comprehensive in-package humidity data, IMPAK offers moisture testing services designed to measure RH levels over time. This proprietary testing regimen is designed to work with simulations of the conditions a customer would expect their package to experience, such as cross-country shipping and wide temperature variations.
How Are Desiccants Rated?
Packaging engineers face a confusing array of variables when selecting moisture adsorbents partly because moisture control is a multifaceted challenge.
There are four sources of water contamination in a closed container or package:
1) the water vapor in the air inside the package
2) the water vapor adsorbed by the materials inside the package
3) the water vapor on the walls of the package
4) and the permeation of water vapor into the package
Historically, desiccants are chosen by application-testing, commonly known as trial and error. The variables can be classified into two main groups:
1) those pertaining to the product, its package and its environment
2) and the various properties of commercially available desiccants
Through firsthand testing and published research, the packaging engineer determines the conditions surrounding optimum product preservation and performance. In attempting to meet and maintain these conditions, one often encounters moisture and its accompanying hazards: corrosion, rust, mold, mildew, fungus, swelling and other undesirable factors affecting product integrity. Where can one turn for answers?
Based upon its wartime experience in the development of food and drug drying agents, the US Department of Defense developed specifications addressing the elimination of corrosion and mildew by adsorbing the moisture from the air of an enclosed space. In November 1963, the DOD released MIL-D-3464C, covering the use of bagged desiccants for packaging and static dehumidification. Three years later, MID-D-3464D served to update the original specification, creating a uniform standard of comparison in a wide variety of areas: adsorption capacity and rate, dusting characteristics of the package, strength and corrosiveness of the package and particle size of the desiccant.
In 1973, the DOD followed with specifications for cleaning, drying, preserving, and packaging of items, equipment, and materials for protection against corrosion, mechanical and physical damage, and other forms of deterioration. MIL-D-3464 and MIL-P-116 have long been the only objective source for packaging engineers. The strength of these specs lies in determining a uniform unit of drying capacity, enabling one to compare desiccant effectiveness on a common scale.
The specifications, however, fail to deal specifically with variables, such as product environment, packaging of the product itself, and the type of desiccant suitable for a specific need. Also, other important factors are defined but not applied: desiccant packaging form, cover stock, adsorption rate, and adsorption capacity. These specifications seem only to compare the conformance of the desiccant selected to Defense Department standards.
As a result, the packaging engineer may be at a loss to choose with confidence which particular desiccant is best for each application. Thus, the engineer must move outside the limited scope of military specifications and into the real world of moisture-proof packaging: the product's environment and package.